D-tech Manufacturing
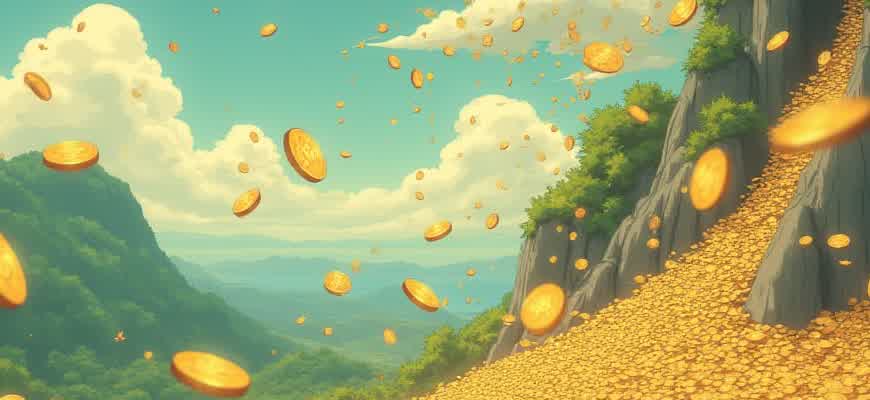
D-tech Manufacturing specializes in the development and production of advanced technological solutions aimed at enhancing manufacturing processes across various industries. By integrating cutting-edge automation and precision techniques, the company has carved out a leadership role in providing scalable, high-quality production services.
The core of D-tech’s approach lies in its ability to leverage modern manufacturing technologies. The company uses a wide range of machinery and software to ensure efficiency and accuracy at every stage of the production process:
- Automated assembly lines
- Advanced robotics
- Custom software solutions for process optimization
- High-precision equipment for quality control
D-tech Manufacturing is dedicated to creating solutions that not only meet but exceed the demands of the global market.
Key aspects of the company's operations include:
- Streamlined production cycles
- Enhanced product reliability
- Commitment to sustainability and resource efficiency
By continuously adapting to the latest trends in industrial technology, D-tech remains at the forefront of innovation in manufacturing.
How D-tech Optimizes Production Time Without Compromising Quality
In modern manufacturing, the balance between speed and precision is a critical factor for maintaining a competitive edge. D-tech Manufacturing has developed innovative strategies to reduce production timelines while ensuring that quality standards are consistently met. Through cutting-edge technology and streamlined processes, the company has found ways to boost efficiency without sacrificing the integrity of the final product.
By leveraging advanced automation, data-driven insights, and continuous process refinement, D-tech has established a system that not only accelerates production but also enhances the precision of manufacturing. These improvements allow the company to meet high-demand production goals while maintaining consistent product excellence.
Key Approaches to Reducing Production Time
- Advanced Robotics: Automation reduces manual labor, minimizing human error and speeding up repetitive tasks.
- Real-time Data Analytics: Continuous monitoring allows quick identification of bottlenecks, enabling immediate corrective action.
- Integrated Supply Chain: D-tech's optimized supply chain ensures faster sourcing and delivery of materials, reducing wait times between production stages.
Production Time vs. Quality: The D-tech Formula
The balance between reducing production time and ensuring product quality is a delicate one. D-tech relies on several key practices to maintain this equilibrium:
- Quality Control Automation: By automating inspections and using high-precision sensors, defects are detected early in the process, preventing costly rework.
- Continuous Improvement Initiatives: Regular assessments of production methods help identify inefficiencies and quality risks, leading to refined processes.
- Employee Training and Expertise: Skilled workers are trained to operate advanced machinery and troubleshoot issues quickly, ensuring minimal downtime.
"By integrating technology at every stage of production, D-tech achieves a level of efficiency that allows us to stay ahead of market demands while ensuring that each product meets our strict quality standards."
Performance Comparison: Traditional vs. D-tech Methods
Aspect | Traditional Manufacturing | D-tech Manufacturing |
---|---|---|
Production Speed | Slower due to manual processes | Faster through automation and data analytics |
Quality Control | Manual inspection, prone to error | Automated, real-time quality monitoring |
Cost Efficiency | Higher due to inefficiencies and rework | Lower, thanks to streamlined processes |
Key Benefits of Customization in D-tech's Product Line
Customization is a core feature of D-tech Manufacturing's product offering, providing clients with tailored solutions that meet specific needs. This adaptability allows for better alignment with industry requirements, leading to higher efficiency and performance. D-tech's ability to create bespoke products ensures a competitive edge in the market by addressing unique challenges faced by various sectors.
By opting for custom solutions, customers gain a strategic advantage. The flexibility in design, materials, and functionality enhances product longevity, reduces operational costs, and boosts productivity. Below are some of the key advantages of customizing D-tech’s products for your business:
Advantages of Product Customization
- Precision Fit: Custom products are designed to meet exact specifications, ensuring a perfect fit within your operations or machinery.
- Enhanced Efficiency: Tailored products are often more efficient, streamlining processes and minimizing downtime.
- Cost Reduction: By addressing specific requirements from the start, customization can reduce waste and unnecessary modifications.
- Future-Proofing: Custom products can be designed with scalability in mind, adapting to future needs and technological advancements.
Customization Process Overview
- Initial Consultation: Understanding client needs and requirements in detail.
- Design Phase: Engineers create a tailored blueprint based on client feedback and specifications.
- Prototyping: A prototype is developed to ensure the product meets all design expectations before full-scale production.
- Production: Once approved, the product is manufactured with the highest quality standards in mind.
Customization offers the opportunity to innovate, providing solutions that are precisely aligned with business goals, reducing inefficiencies, and maximizing output.
Key Features of Customized Products
Feature | Benefit |
---|---|
Material Selection | Choose materials that optimize performance and longevity for specific applications. |
Design Flexibility | Products can be tailored to specific space, size, or aesthetic requirements. |
Integrated Technology | Incorporate advanced features like IoT connectivity or automation, if required. |
Assessing the Durability and Longevity of D-tech Products
Ensuring the longevity and durability of products manufactured by D-tech requires rigorous testing and evaluation. These products are designed to withstand demanding environments and long-term usage. Several methods are employed to assess their endurance, from material strength testing to real-world stress simulations. Regular assessments help in optimizing the performance and lifespan of each product, ensuring that they meet industry standards and customer expectations.
Key to these assessments are parameters such as resistance to wear, impact resilience, and fatigue strength. Understanding how each component reacts under pressure allows for improved designs that extend the product's useful life. Below are the primary tests and methods used to evaluate durability:
Testing Methods
- Accelerated Life Testing (ALT): Simulates prolonged usage in a shortened time frame by subjecting the product to extreme conditions.
- Environmental Stress Testing: Evaluates how the product performs under temperature fluctuations, moisture, and other environmental factors.
- Load and Impact Resistance: Measures how well the product can withstand physical forces, such as pressure, shock, and impact.
Factors Contributing to Durability
- Material Composition: The quality and type of materials used directly affect the product's resilience to wear and tear.
- Design Integrity: Well-engineered designs reduce stress concentrations and enhance the product's overall durability.
- Manufacturing Process: Precision in production methods ensures consistent quality, minimizing the chances of defects that could shorten the product’s life.
"D-tech products are crafted with a focus on longevity, using advanced technologies and high-quality materials to ensure that they perform reliably over time."
Key Durability Metrics
Test Type | Performance Metric | Expected Result |
---|---|---|
Accelerated Life Testing | Cycle Count | 100,000+ cycles without failure |
Environmental Stress Testing | Temperature Range | -40°C to 85°C without degradation |
Load and Impact Resistance | Impact Resistance | Withstands 1,000+ impacts without structural failure |
The Cost-Saving Advantages of Collaborating with D-tech Manufacturing
Partnering with D-tech Manufacturing offers businesses a strategic path to reduce operational costs and enhance overall efficiency. By leveraging cutting-edge technologies and expertise, D-tech helps streamline production processes, resulting in significant savings. Whether it's optimizing labor, reducing material waste, or improving supply chain management, D-tech's solutions drive down costs while maintaining high-quality standards.
With a focus on long-term partnerships, D-tech offers tailored services that can accommodate various industries, ensuring a competitive edge. The combination of advanced automation, industry-specific know-how, and a commitment to cost-effective solutions makes D-tech an invaluable partner in the manufacturing sector.
Key Cost-Saving Opportunities
- Process Automation: Implementing automated systems can significantly reduce labor costs and enhance consistency in production.
- Efficient Resource Utilization: D-tech's advanced analytics help optimize the use of raw materials, minimizing waste and maximizing output.
- Supply Chain Optimization: Streamlining logistics and inventory management reduces overhead and ensures timely delivery, avoiding costly delays.
- Energy Efficiency: D-tech's energy-saving initiatives cut down utility costs, contributing to overall expense reductions.
Potential Savings Breakdown
Area of Improvement | Estimated Savings |
---|---|
Labor Costs | 20-30% |
Material Waste Reduction | 15-25% |
Logistics & Supply Chain | 10-20% |
Energy Consumption | 5-10% |
"By optimizing production flows and embracing innovative solutions, D-tech allows companies to reduce costs while improving efficiency and quality."